
- #Axisymmetric condition plaxis 2d anchor verification
- #Axisymmetric condition plaxis 2d anchor software
For geotechnical works in mines and quarries, it there is not today's general methodology for analysis and the quantification of the risks relating to the dangers inherent in these concrete types (falling boulders, landslides, etc.). The study of the stability of the mining works in rock masses fractured is the major concern of the operating engineer. The developed 3D Particle method was able to simulate the 3D large deformation of soils due to soil yielding and calculate the variation of normal and shear stresses following clay deformation.
#Axisymmetric condition plaxis 2d anchor software
The results were also compared with those of a commercial FEM software PLAXIS 3D. First of all, an unconfined compression test was carried out and the large deformation following soil yielding or failure was simulated by the developed 3D Particle method. The yielding and hardening behavior of soil before failure was also considered by varying viscosity of soil. The Mohr-Coulomb failure criterion was incorporated into the 3D Particle method to determine soil failure. In the 3D Particle method, the governing equations were discretized by various particle interaction models corresponding to differential operators such as gradient, divergence, and Laplacian. Oai:tudelft.In this study, a three-dimensional (3D) Particle method without using grid was developed for analyzing large deformation of soils instead of using ordinary finite element method (FEM) or finite difference method (FDM). For future research, it is still advised to… Refine mesh requires a lot more time for calculation. Coarse mesh leads to low accuracy results that certain stress points receiving much high stress than it should. The mesh set-up is also crucial to 3D FEM model. It is advised to apply 3D FEM model when dimensions and shape of the excavation zone allows the model to maximize the corner effect. This is because the sheet pile wall can benefit from the corner effect in 3D scenario. If the section length was lowered from 50m to 30m, the bending of sheet pile wall could be reduced by 20%. If the excavation section was longer than 50m, the whole domain can be considered as plain strain, so that the results in 2D and 3D FEM models were almost the same. The parametric study of 3D FEM model showed that the geometry of the excavation zone and the mesh set-up has great influence over the response of sheet pile wall. The responses of sheet pile walls as well as surrounding soil were recorded and compared with results from normal 3D excavation model. Different excavation rates, excavation directions and lateral support design were tested in order to optimize the sequential excavation model. After the comparison between 2D and 3D FEM model, the sequential excavation method was implemented into 3D FEM model. The excavation was designed to be dry excavation. The excavation method applied in 2D and 3D FEM model was normal staged excavation. Certain geometry (50m * 18m) of excavation section was determined so that the results from 3D FEM model and 2D FEM model were comparable. Parametric study was done in order to investigate how the domain and mesh set-up influence the results in 3D FEM model. The 3D FEM model adopted the model set-up tested and adjusted in 2D FEM model. The deflections of sheet pile walls in both 2D models were at similar level. The soil and building material parameters were first tested in 2D spring model and 2D FEM model.
#Axisymmetric condition plaxis 2d anchor verification
Instead, 2D models were made for comparison and verification purpose.
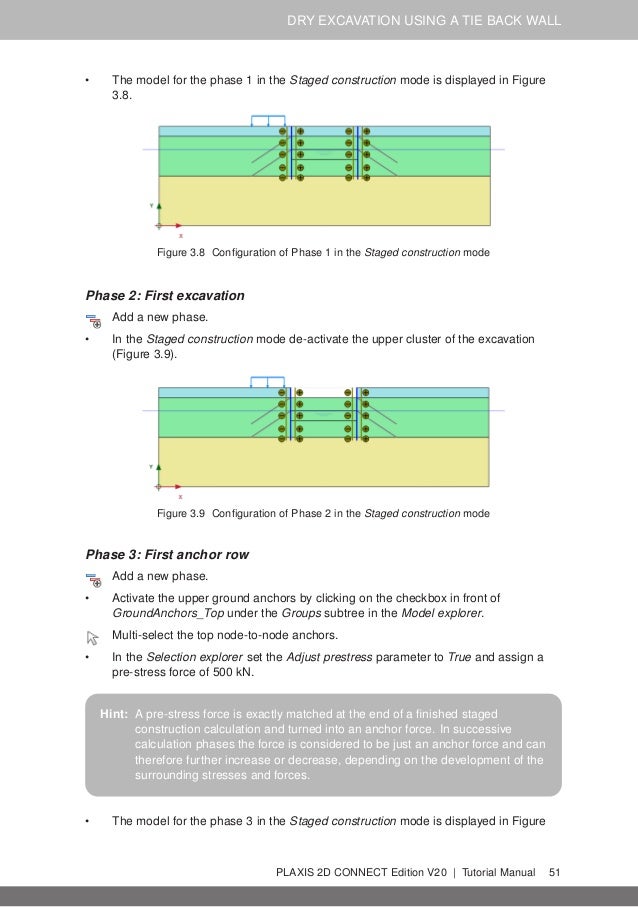
Since the construction of Spaarndammertunnel starts after the completion of this graduation project, no field data was available for verification. The research focus was to investigate the advantages and disadvantages of applying 3D FEM modelling for deep excavations.

The data for soil investigation and preliminary design were provided by CRUX Engineering BV. The excavation plan, retaining structure and building material were developed from the preliminary design of this project. The soil data was compared with Amsterdam North-South metro line database as well. Cone penetration tests and boreholes were carried out along the tunnel location. Soil parameters used in models were derived from in situ soil investigation. This thesis only focused on the excavation part of the tunnel project. It is an independent research project based on the Spaarndammertunnel project in Amsterdam. This thesis discusses the use of 3D finite element method (FEM) in deep excavations, especially the simulation of sequential excavation method in 3D FEM model. 3D FEM analysis for sequential excavation
